
The AESTUS recurve riser is named after the upper stage engine of the same name for the European Ariane rockets. The term comes from Latin and can be translated as embers or heat. The engine is specially optimized for vacuum requirements, where it achieves a thrust of 28400 N at an output of 43700 kW. It was developed in Ottobrunn near Munich and has transported the ATV to the ISS.

VEGA is a European launch vehicle for transporting small satellites and Cubesat constellations into low-Earth orbit. Its construction is extremely robust. The first stage achieves a maximum thrust of 3040 kN.
Sustainable!
We also pay special attention to sustainable production when manufacturing our equipment. By purchasing our high-quality equipment, you can contribute to environmental and climate protection. Not only the components manufactured in-house, but also all purchased components, tools and accessories come from German production facilities. E.g. even our high quality textile bags for the riser are made by a tailor shop in Aachen. In this way, transport distances are short and CO2 emissions are low. Our own workshop uses 100% green electricity. In addition, we use plastic-free packaging or recycled plastic wherever possible. We also use ecological alternatives as filling and upholstery material or reuse the upholstery material, which we receive ourselves from our suppliers.
- Local production with short transport distances
- Environmentally friendly packaging
- Accessories from German production
- 100% green electricity
F.L.A.T. – Form Locking Alignment Technology
Ideal force transmission due to form locking (Form Locking)
Maximized contact area between limb and center section
Power transmission distributed over a large area
Reduced shock
Both the tiller screw and the dovetail bearing are rotatably mounted. The head of the tiller screw and the dovetail bearing adapt to the angle of the limb in every tiller position. In this way, a large area of contact between the limb and the components of the riser is always guaranteed. The distribution of the load over a larger contact area leads to a reduction in stress peaks in the limb pocket, which results in a smoother bow reaction when the shot is fired. In addition, the contact surfaces on the limb are protected, thus increasing the service life of the components.
With a rigid tiller screw (even those with a tilting head), the limb also introduces lateral forces and thus a bending force into the tiller screw. These lateral forces have to be absorbed by the riser via the thread of the tiller screw, which generally represents an unfavorable load for a thread. In addition, the threads for the tiller screws are usually cut directly into the aluminum of the riser. The material mix of steel tiller screw and aluminum thread already leads to an unfavorable power transmission, because the steel is much stronger than the aluminum. In addition, many tiller screws are secured with an expanding screw. The steel thread of the tiller screw literally digs into the aluminum thread and can lead to permanent damage.
In contrast, the tiller screw with the F.L.A.T. system is only subjected to a tensile force due to the rotatable bearing. This ensures lower forces in the screw and lower stresses when force is transmitted to the riser. In addition, the stainless steel tiller screw is mounted in a bolt made of the same material. Thus, only identical material pairings are used for threads. The force transmission to the riser takes place via the form fit between the bolt and the aluminum body of the riser, so that a larger area is effectively used for application of the force.
Ideal force transmission due to form locking (Form Locking)
Maximized contact area between limb and center section
Power transmission distributed over a large area
Reduced shock
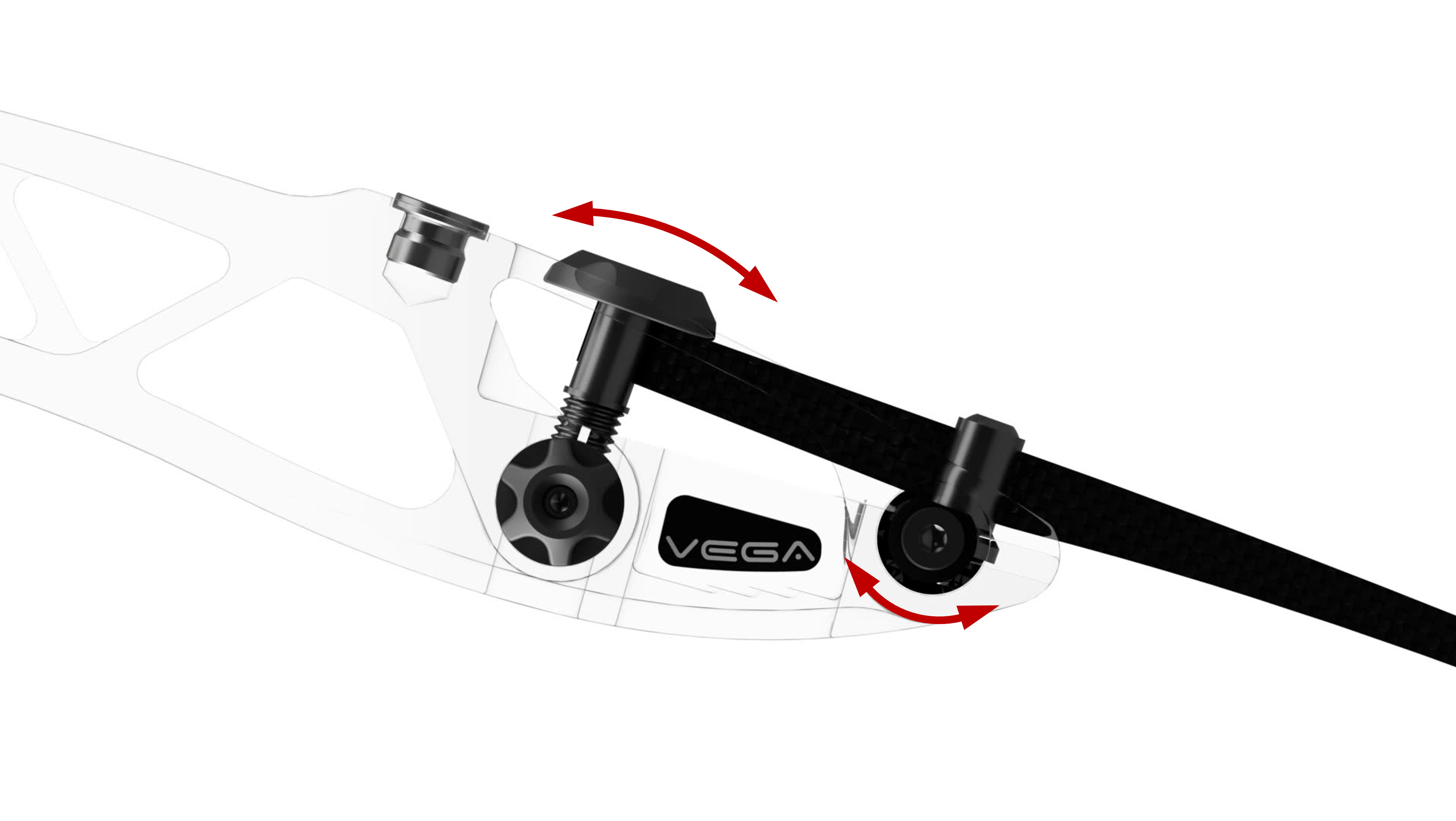
Both the tiller screw and the dovetail bearing are rotatably mounted. The head of the tiller screw and the dovetail bearing adapt to the angle of the limb in every tiller position. In this way, a large area of contact between the limb and the components of the riser is always guaranteed. The distribution of the load over a larger contact area leads to a reduction in stress peaks in the limb pocket, which results in a smoother bow reaction when the shot is fired. In addition, the contact surfaces on the limb are protected, thus increasing the service life of the components.
With a rigid tiller screw (even those with a tilting head), the limb also introduces lateral forces and thus a bending force into the tiller screw. These lateral forces have to be absorbed by the riser via the thread of the tiller screw, which generally represents an unfavorable load for a thread. In addition, the threads for the tiller screws are usually cut directly into the aluminum of the riser. The material mix of steel tiller screw and aluminum thread already leads to an unfavorable power transmission, because the steel is much stronger than the aluminum. In addition, many tiller screws are secured with an expanding screw. The steel thread of the tiller screw literally digs into the aluminum thread and can lead to permanent damage.
In contrast, the tiller screw with the F.L.A.T. system is only subjected to a tensile force due to the rotatable bearing. This ensures lower forces in the screw and lower stresses when force is transmitted to the riser. In addition, the stainless steel tiller screw is mounted in a bolt made of the same material. Thus, only identical material pairings are used for threads. The force transmission to the riser takes place via the form fit between the bolt and the aluminum body of the riser, so that a larger area is effectively used for application of the force.
Dual lateral adjustment – Advanced adjustment options (Alignment)
NOVAERY’s AESTUS and VEGA are the world’s first recurve riser to be launched on the market with a dual system for lateral adjustment through the F.L.A.T. system. This allows not only precise alignment of the bow, but also parallel displacement of the limb in the limb pocket. Many limbs are made straight in themselves, but the hole for the dovetail or the groove for the tiller screw are not 100% centered. With the F.L.A.T. system, these tolerances can be fully compensated.
- Primary lateral adjustment: The limb can be positioned continuously and exactly centrically via the adjustment screws on the side while the bow is strung. To do this, the bolt is moved laterally with the Tiller screw via an M6x0.5 fine pitch thread. One revolution corresponds to 0.5 mm of lateral movement. The maximum adjustment range is up to +/-1.5 mm.
- Secondary lateral adjustment : The dovetail bearing offers a classic shim system. With an adjustment range of +/- 1 mm, the limb can be adjusted in 0.1 mm increments.
Dual lateral adjustment – Advanced adjustment options (Alignment)
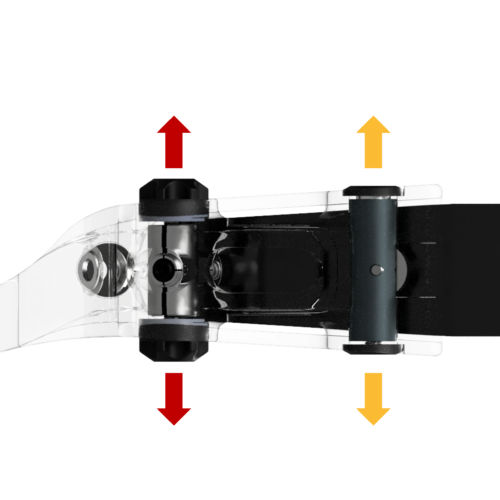
NOVAERY’s AESTUS and VEGA are the world’s first recurve riser to be launched on the market with a dual system for lateral adjustment through the F.L.A.T. system. This allows not only precise alignment of the bow, but also parallel displacement of the limb in the limb pocket. Many limbs are made straight in themselves, but the hole for the dovetail or the groove for the tiller screw are not 100% centered. With the F.L.A.T. system, these tolerances can be fully compensated.
- Primary lateral adjustment: The limb can be positioned continuously and exactly centrically via the adjustment screws on the side while the bow is strung. To do this, the bolt is moved laterally with the Tiller screw via an M6x0.5 fine pitch thread. One revolution corresponds to 0.5 mm of lateral movement. The maximum adjustment range is up to +/-1.5 mm.
- Secondary lateral adjustment : The dovetail bearing offers a classic shim system. With an adjustment range of +/- 1 mm, the limb can be adjusted in 0.1 mm increments.
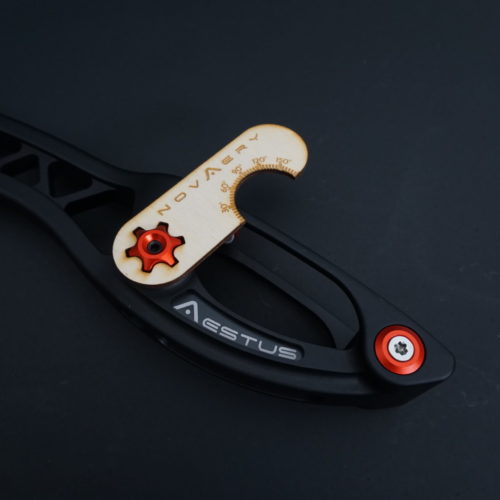
Unique surface
Scratch resistant
Durable
Robust
The surface finish plays a major role in quality. Look, feel, toughness and durability are the most important criteria. That’s why we use a extreme durable and robust hard anodizing finish for our recurve riser, which was specially developed for the high-strength alloy EN AW 7075. This layer is thicker and harder than standard anodizing processes and also outperforms DIN standard hard anodizing processes. Before anodizing, the riser are blasted with glass beads and then stained again. This creates a matte, homogeneous, smooth surface. Of course, our center parts are available in different colors. Since the aluminum alloy EN AW 7075 causes a strong inherent coloration during anodizing, which becomes more intense with increasing layer thickness, the layer thickness must be reduced somewhat for bright colors. Thus, the resistance is still above the level of ordinary decorative anodized coatings. We achieve the most robust surfaces in the colors black and nature.
Individual look
Stand out from the crowd!
The aluminum add-on parts are made of the same alloy as our stabilizer components. Therefore, these are also available in up to 10 different colors. In this way, the look of the entire bow can be put together according to your individual ideas and, for example, the TERRA stabilizer can also be matched to the recurve riser design.
In addition, exclusively in the Premium Package, we offer to individually engrave two of the four logo emblems in the litter arm pockets. For example, you can mark your centerpiece with your name.
TORX
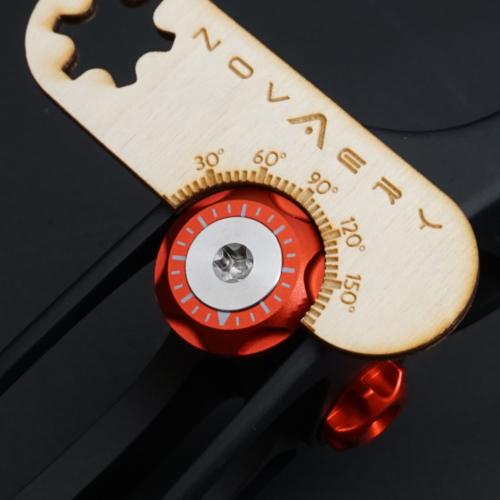
Who hasn’t it happened to? Once you’re not paying attention, you take the wrong Allen key in the confusion of inch and metric threads on the bow. If bad luck is also involved or a screw is stuck, the hexagon socket is quickly rounded. What now? Only screws with a TORX drive are installed in our recurve riser. The advantage, there is no metric or inch TORX. The sizes are the same for both threads. “Round turning” is almost impossible as long as the screw is tightened by hand.
Stainless steel stabilizer thread
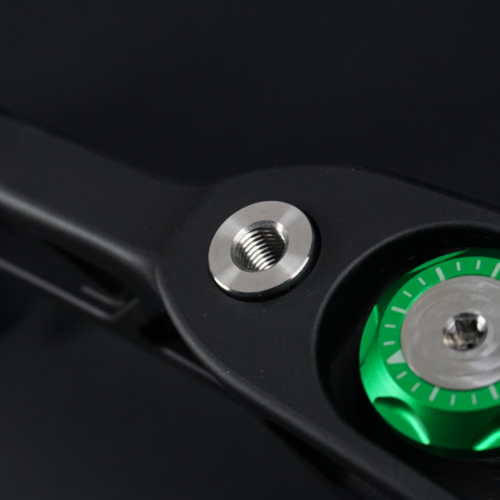
We manufacture the threaded inserts for the stabilizers out of stainless steel. This ensures a rock-solid connection between the stabilizer and the riser. In addition to the front thread, we also paid special attention to the secondary thread inserts during development. More and more shooters mount here not only dampers, but also the V-bar to freely design the system according to their own wishes. For this reason, these threaded inserts with a diameter of 15.5 mm have a particularly large contact surface for optimum locking.
Laser engraving
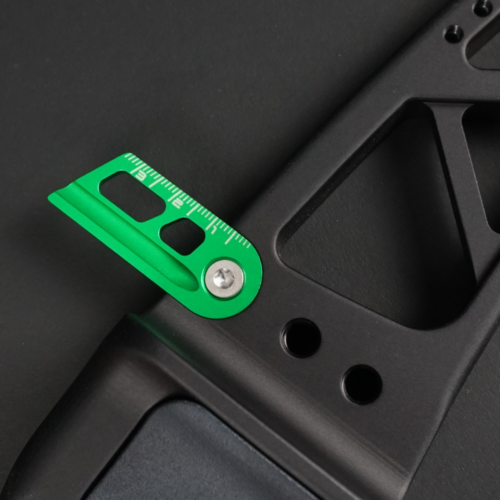
A scale accurate to the millimeter is engraved into the head of the tiller screw and the clicker plate using a CO2 laser. In this process, only the color pigments in the anodized layer are destroyed by the heat of the laser; the protective layer itself remains completely intact. In this way, the bow can be adjusted in a reproducible manner. Different clicker or tiller positions can be noted for different arrows or limbs. This simplifies the changeover when changing equipment, for example from summer to winter season.
Individual grip thanks to innovative technology
Our grip technology is unique to date. The grips are manufactured using the SLS (selective laser sintering) 3D printing process. A thin layer of extremely fine powder is applied to a base plate by machine. A laser beam is then used to melt the area in this layer that will later become part of the component. The laser practically scans the component pixel by pixel in this cutting plane. The remaining area remains as loose powder. The next layer of powder is then applied, which is again melted in spots. In this way, the component grows layer by layer. At the end, the grip is in a cube of powder. This is shaken off on a grid and the grip remains. The remaining powder can be reused for new prints, so no waste is created during production.
The result is a monolithic component with a rough surface. The individual layers are hardly recognisable compared to ordinary FDM 3D printing and the adhesive force between the layers is just as high as in the plane. This results in a much higher strength. The component surface can then be smoothed and coloured in various post-processing steps.
SLS technology enables new design freedom for grips. Design elements are possible that were previously not realizable. Grips can be customised even for small quantities because no moulds are needed or machines set up. The surface can be left rough or smoothed for maximum slip resistance. Rain or sweat are also no problem. The surface is open-pored at µm level and thus permeable to water. This prevents the formation of a fluid layer between the skin and the grip surface. The water is absorbed by the material like a sponge and dries again later. This means that the surface adhesion never changes, regardless of whether the grip is wet or dry.